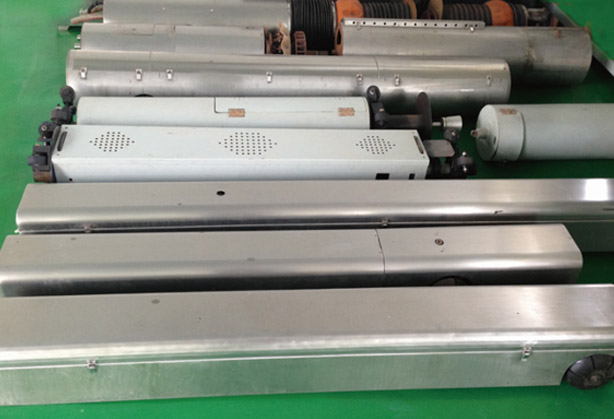
Aiming at the fine anticorrosion of pipe welding mouth,Dacang designs and manufactures robots for pipe internal girth weld rust cleaning, coating, holiday repair and detection, including:
1 - shot blasting robot,2 - steel wire impact-type rust cleaning robot, 3 - weld junction cleaning robot,4 - epoxy powder/ liquid coating and repairing robot,5 - 1.internal anticorrosion detection robot.
Forstorage tank and ship anticorrosion,Dacang also developed robot technology:
1 - Detecting robot for storage tank and ship; 2 - Rust cleaning robot for storage tank and ship.
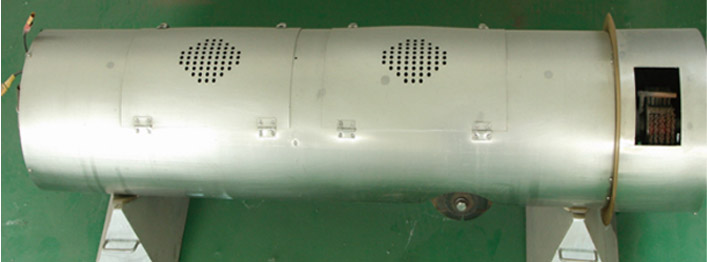
Steel wire impact-type rust cleaning robot
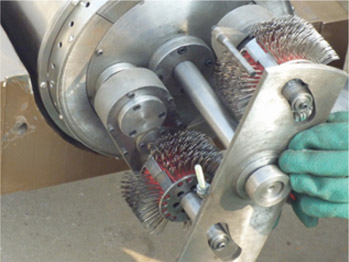
Steel wire impact-type rust cleaning robot
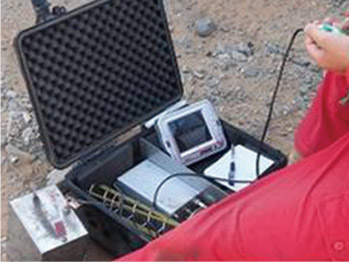
Remote control system for robot
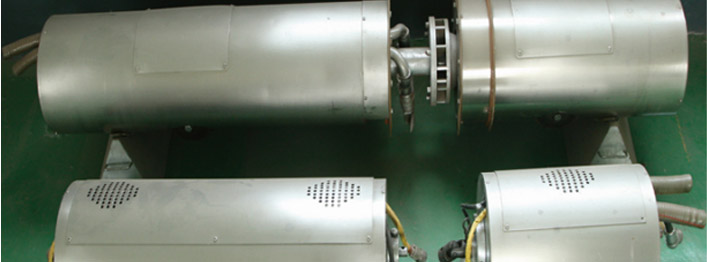
Shot blasting rust removal robot
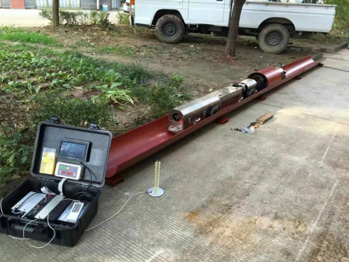
Internal welding robot
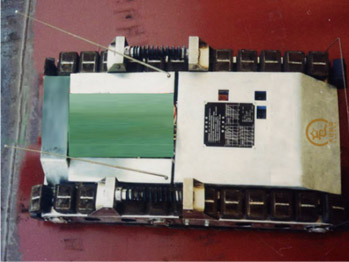
Detecting robot
PICKLING
With the further development of pipeline anticorrosion technology, the acid washing of pipes before anticorrosion has attracted more and more attention from home and abroad in recent years. Especially in the overseas anticorrosion engineering, if there is no pickling process, the steel pipe anti-corrosion production line will be avoided. In order to meet the demand of pipeline anticorrosion quality improvement at home and abroad, Qingdao Dacang Anticorrosion Co., Ltd. has used more than three years to develop an on-line pickling device on the outer surface of the steel tube. A complete system has been formed from the production of pure water dispensing- acid cleaning - water washing - air drying - acid mist purification - waste water purification, recycling, and up-to-standard discharge. To provide technical and equipment support for on-line pickling of steel pipe outer surface.
It is suitable for the wide range of pipe diameter and high production efficiency.
Use phosphoric acid cleaning fluid to reduce damage to human body and environmental pollution.
The waste liquid can be recycled and reused. At the same time, it can achieve the discharge of the standard.
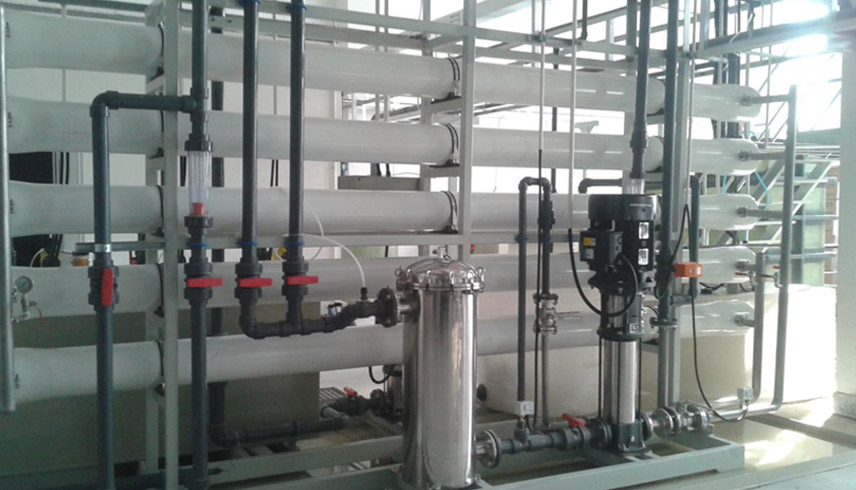
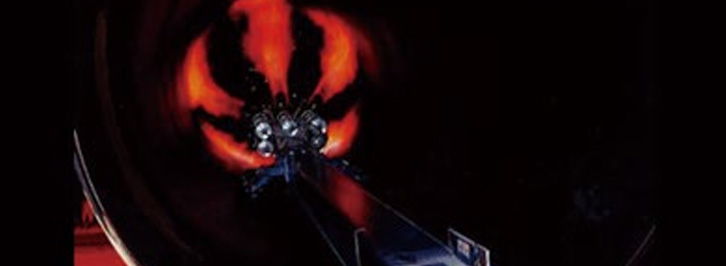
Function: heating the surface of the steel pipe to the required temperature except for the moisture and oil stains on the surface of the steel pipe.
Composition:flame distributor, gas pipeline system, combustion supporting fan, mobile system, electric control cabinet.
Working principle:preheating the steel pipe before rust removal by natural gas burner. The burning head of the front end of the support rod is inserted into the tube, the flame is heated directly to the tube wall, and the steel pipe is rotated during the heating process to ensure that the heating is uniform and the sealing room of the two ends of the steel pipe is set respectively, so as to ensure the flame is not escaping during the heating process. The flame is not easy. The vent and fan are installed at the top of the The air vent and fan are installed at the top of the sealing room, and the flue gas generated by the combustion process is discharged through the ventilation pipe.
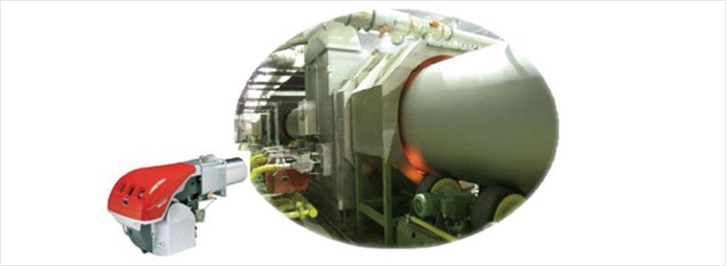
Function:preheat the surface of the steel tube.
The system is mainly composed of burner, preheating furnace, chimney, electric cabinet and so on. The working principle is the flame collection of the burner during the preheating process of the steel pipe. The heat is fully utilized by heating from the bottom of the pipe and rotating along the tube.
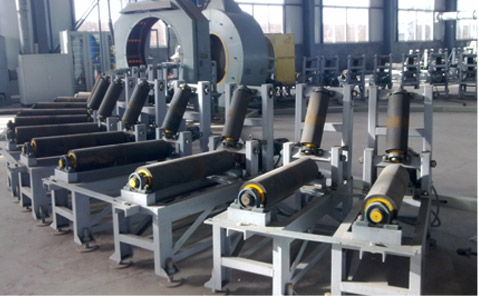
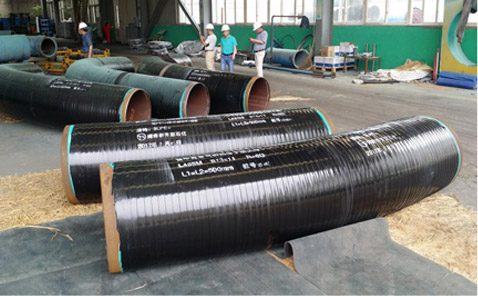
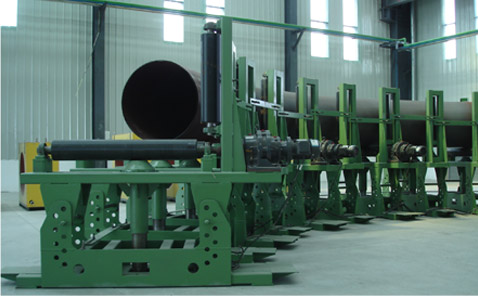
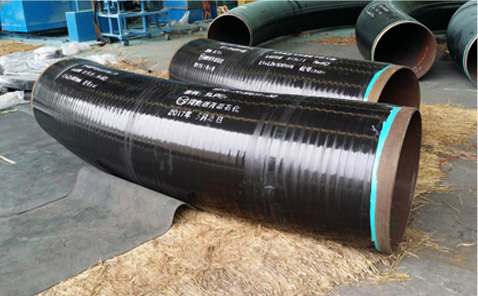
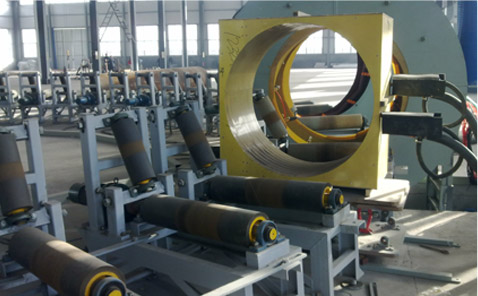
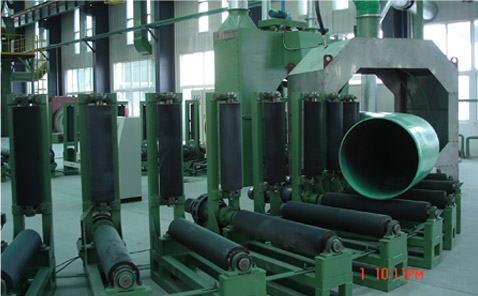
By this brand new technology, integral functions including shot blasting cleaning, anticorrosion, thermal insulation can be realized at one production line, and the four layer structure (anticorrosion layer, thermal insulation layer, adhesive layer and protecting layer) is strengthened.
Steel pipe shot blasting cleaning Liquid or FBE powder coating
PU foaming of thermal insulation layer
Copolymer adhesive twining
PE hot twining
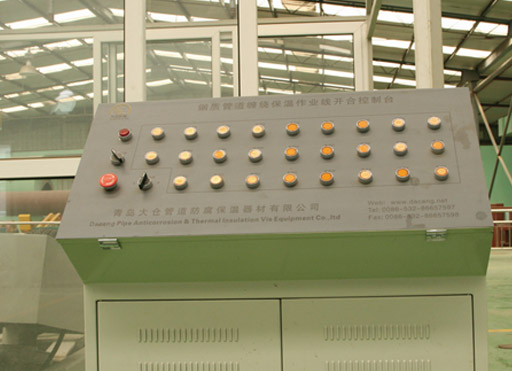
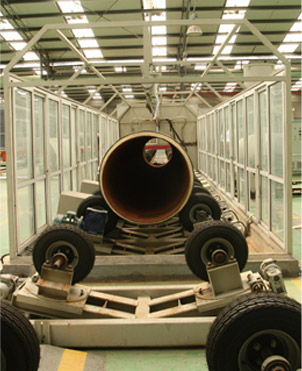
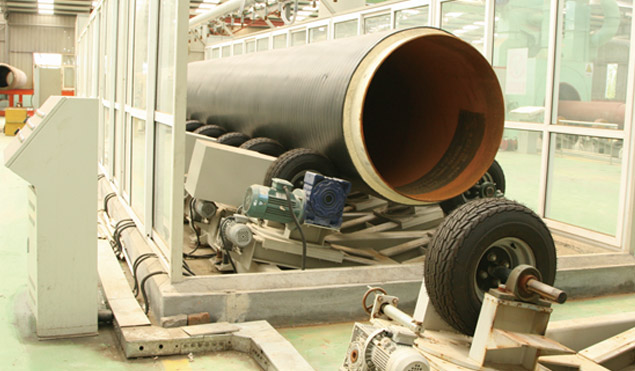
- 1
Poan adhesive twining, PE protecting layer twining is realized at one time, the working process is smooth for automatic production,which save manpower, time, and is easy to operate.
- 2
In case of partial water seepage in the insulation layer, the acidic medium produced by water and polyurethane cannot corrode the surface of the steel tube.
- 3
Copolymer is used for combining the foam layer and PE protecting layer, which makes the bonding performance reinforced.So as to ensure the integrity of the multilayer process and synchronous reliability. The problem of shelling is solved and the problem of water inflow due to the expansion and contraction of the jacket layer is solved. Even if the outer covering of polyethylene is damaged, it will not be threaded.
- 4
The new process adopts spray foaming, and the foaming holes are uniform and fully solidified and hardened. The foaming quality is visible throughout the whole process, and the resulting gas can be released freely without forming flocs or bubbles in the pipe.
- 5
The copolymer adhesive layer and the polyethylene layer were finished by the thermal winding process. The original axial stretching molding was replaced by the present radial stretching molding. It changed the direction of molecular structure of outer sheath PE and effectively eliminated the problem of PE layer and thermal insulation layer shelling.
- 6
The new process automatic operation line is simple and convenient to adjust, and the thickness of the foamed layer and the thickness of the PE layer can be adjusted easily. The production process does not need to change the mold, a variety of pipe diameter (from Φ426 to Φ1620), a variety of thickness of the insulation pipe can be completed on a single line, and more suitable for large diameter pipe.
- 7
Due to the winding process, it is not necessary to make the jacket layer too thick, which can save polyethylene material. The free foaming process will not form a 2-3mm hard shell compared with the old process, which can save polyurethane materials.
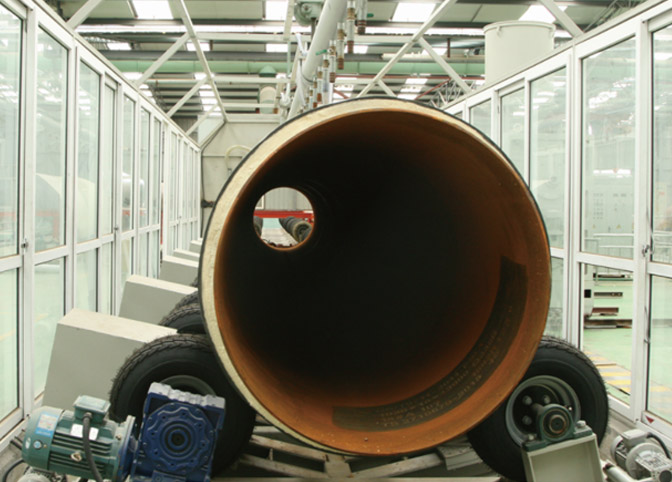
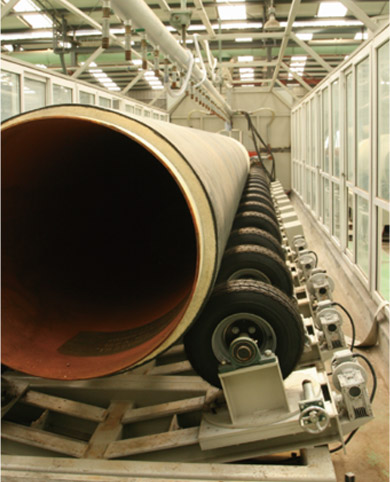
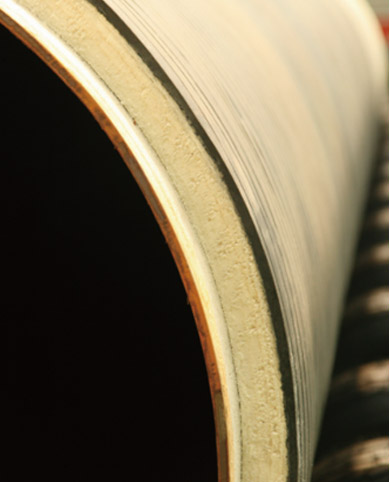
The technology of epoxy powder spraying in the pipeline, because of the high voltage electrostatic spraying, the current market is generally adopted by the Venturi pump spraying process, the powder rate has been hovering around 50%, especially the diameter of more than 500 millimeter steel pipe is lower. The powder recovery is large and the overflow powder is serious. In order to change the current situation and meet the domestic and foreign customers' pursuit of increasing powder rate, Qingdao Dacang Anticorrosion Co., Ltd. has successfully developed a new generation of epoxy powder spraying technology in the pipeline for nearly two years, with a high powder rate of up to 95%. Technological innovation and technological breakthroughs provide strong support for the new generation of epoxy powder spraying technology in pipelines.
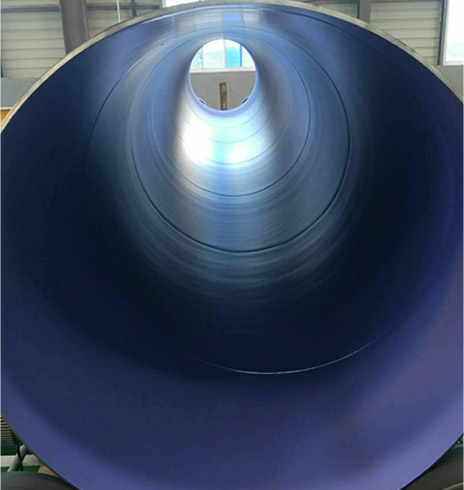
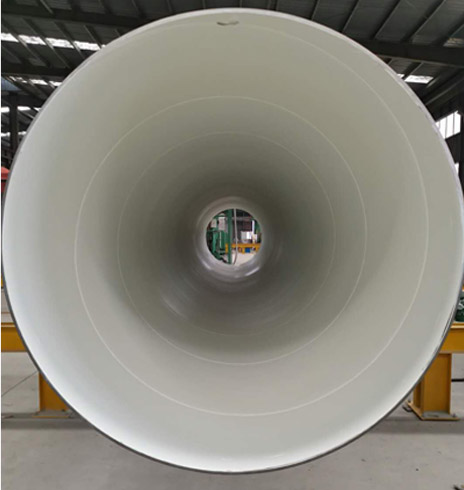
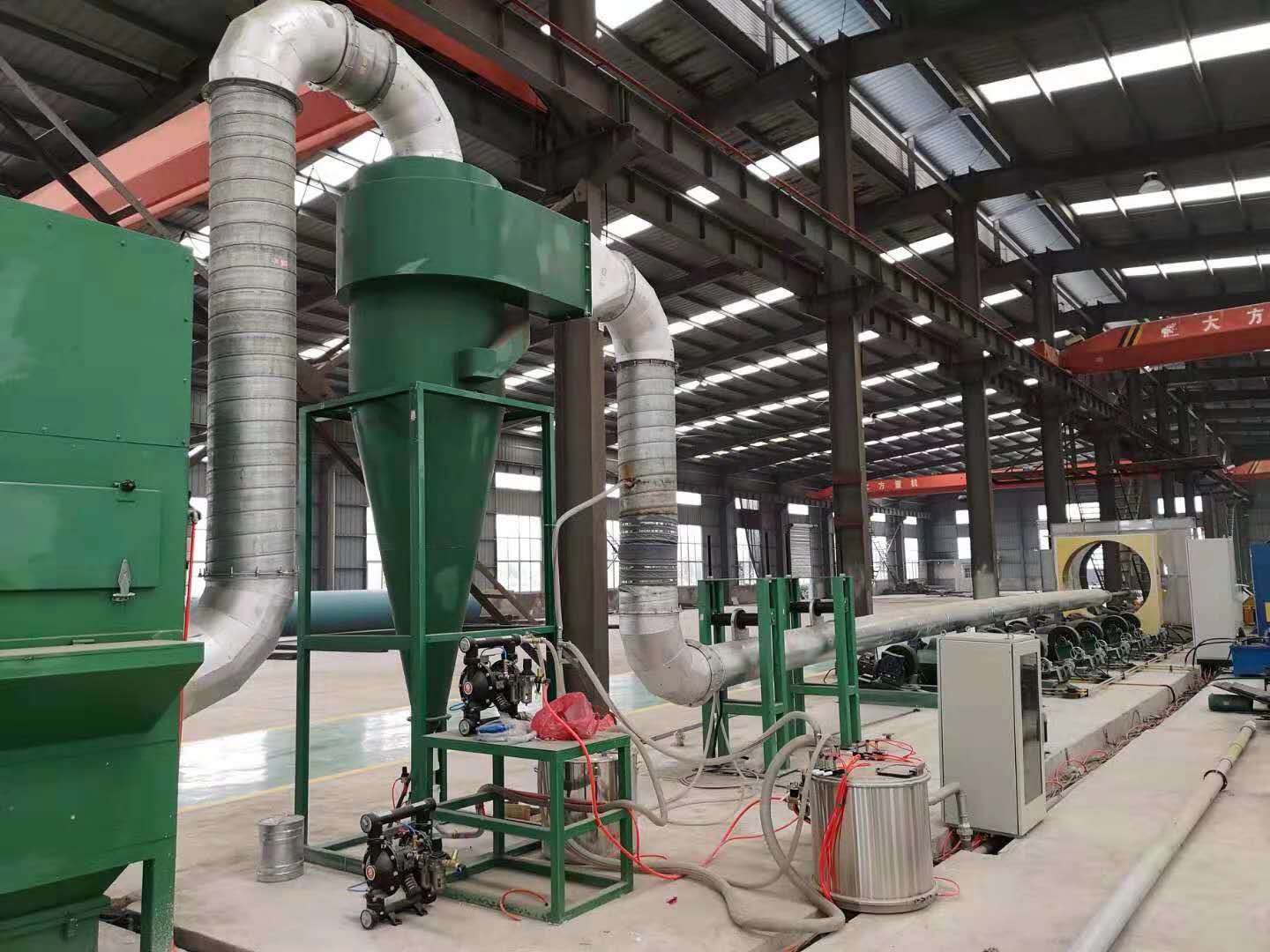
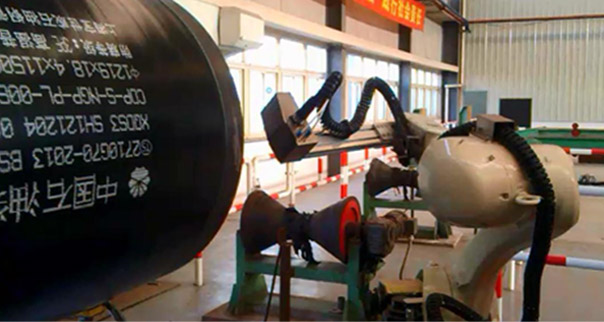

In order to comply with the development of science and technology, improve the production efficiency and quality of the steel pipe anticorrosion production line, reduce the production cost, reduce the number of operators and enhance the safety, our company has developed a full-automatic steel pipe anticorrosion production line.
The automatic steel pipe anticorrosion production line is a revolutionary upgrading, innovation and development of the widely used steel pipe anti-corrosion production line mode. The automatic production line promotes, improves and consummates the mechanical properties of the traditional production line. On this basis, a new automatic control system (ACSOSAP) for steel pipe anticorrosion production is added to realize the automatic production of the steel pipe anticorrosion production line.
The automatic control system for steel pipe anticorrosion production (ACSOSAP) consists of industrial control machine (PC), industrial programmable controller (PLC), touch screen (HIM), frequency converter, industrial Ethernet, SCADA configuration software, and modular production line automatic control software. The internal and external rust removal production line, 3PE process production line, internal and external FBE process production line, internal and external spray paint technology production line, bare pipe line, finished product pipe line, semi finished product transfer, pickling passivation, injection standard, on-line inspection are realized.
The automatic control system (ACSOSAP) for steel pipe anticorrosion production is mainly divided into two levels: workshop monitoring layer and field equipment layer. Workshop monitoring layer realizes the monitoring of workshop level equipment, which includes on-line monitoring of production equipment status, equipment fault alarm and maintenance, production statistics, production scheduling, data analysis and early warning, production information storage and upload. This layer is mainly composed of industrial computer (PC), industrial programmable logic controller (PLC), SCADA configuration software and industrial Ethernet.
The field device layer implements devices that are mainly connected to the on-site production line, such as distributed I/ O, drives, actuators, sensors, intelligent meters, etc. Complete the process control and chain control of the production line, and the operation status of the production line and the collection and uploading of production information. The layer is mainly composed of industrial programmable logic controller (PLC), touch screen (HIM), frequency converter and modularized control software.
When switching pipe according to different diameter of steel pipe in traditional coating production line,it is done by manpower, which wastes time and is concerned with safety. This new patent technology can be automatic opening and closing according to pipe diameter, without manual work.
It has the advantages as following:1. High automatic performance, improving productivity.
2. Reducing labor intensity, and improving, safety.
3. The roller wears evenly in long term use, stable conveying, ensuringcoating quality.
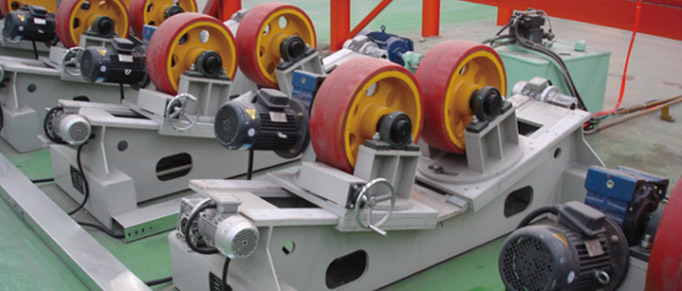
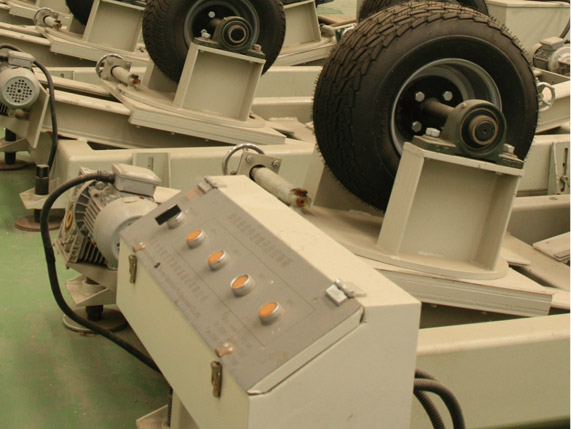
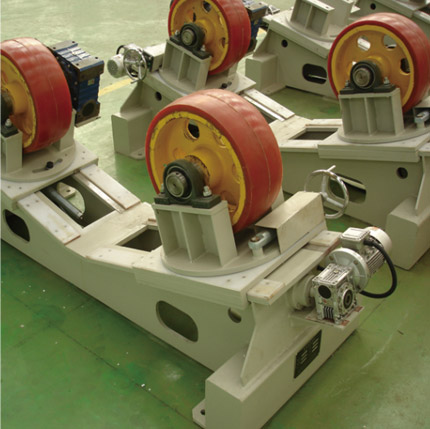
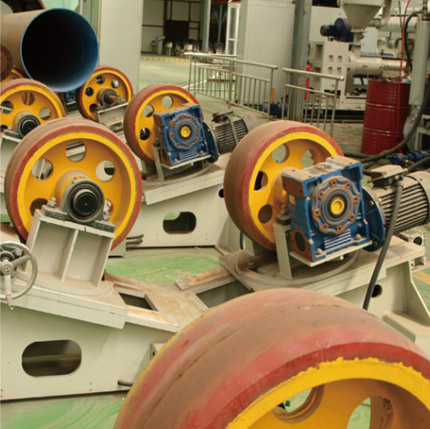
It is the first patented product in the world. It is suitable for simultaneous rust removal and internal and external corrosion protection of various caliber steel pipes, which greatly improves production efficiency and reduces cost.
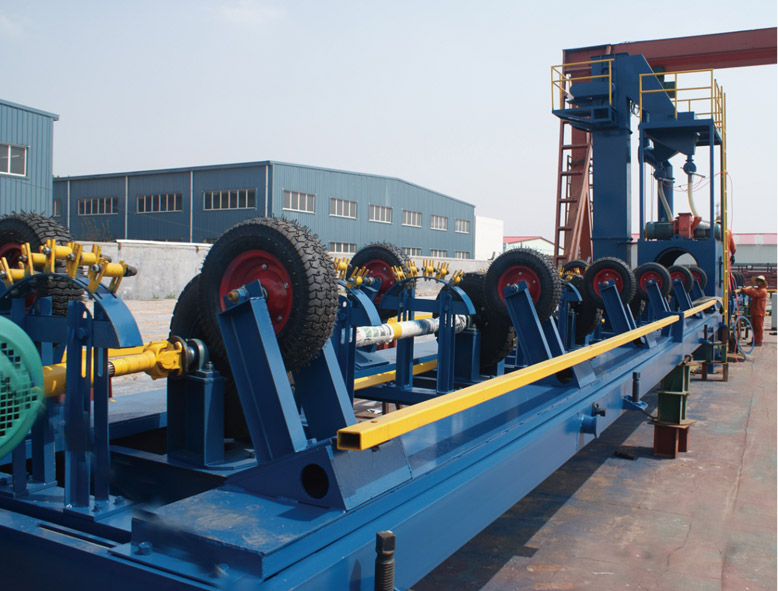
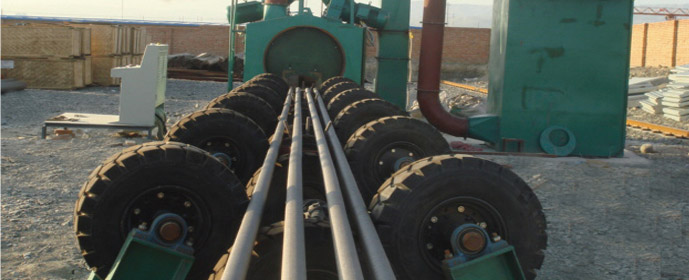
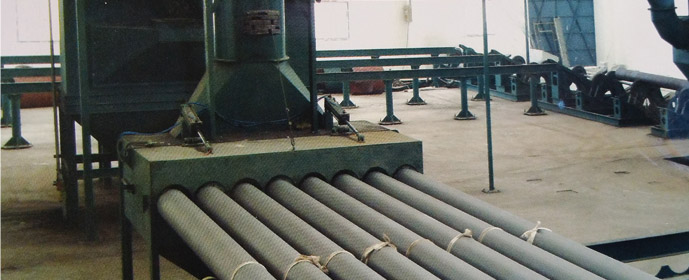